Inspection providers are making tank inspections safer and maintenance and survey schedules more effective with each innovation. But how does Class fit into all of this? And are these technologies equivalent to a surveyor inspecting a tank?
Technological advances are improving the safety of tank inspections by limiting the need for human entry into dangerous conditions. Robotically-operated cameras, for example, can also offer better imagery and data about an asset, feeding into the risk-based inspection (RBI) plan, helping class societies and operators understand the state of their asset, improve planned maintenance schedules and in some cases extend the life of an asset. But are these new innovations safe? And are they accepted by class societies and regulators? Important questions raised by operators as we move towards a more digitalised world.
For many years, LRQA has been working with clients and different technology vendors in the use of remote inspection techniques (RIT), including drones and cameras, on surveys and in developing the equipment. In this article, we focus on one vendor in particular, EM&I Alliance Group, and its ‘NoMan’ camera, and how the company’s technology has changed the way the industry approaches tank inspections, LRQA's involvement in making the technology suitable for surveyors and operators, and what the future holds for this technology.
As many will know, tanks are large, dark spaces with structure that is not easily accessible. So, the traditional approach involved flooding tanks and inspecting via inflatable boats. “Inspection has now evolved from flooding tanks to scaffolding, rope access and walkways, all of which are time consuming, expensive and have multiple safety risks associated with them as they involve putting people into confined, dangerous spaces,” noted Danny Constantinis, Executive Chairman at EM&I Alliance.
“Before scaffolding or rope access was set up, crew members needed to make sure the tank was suitable for personnel to enter, ensuring the tank was gas-free and cleaned so areas were visible and accessible, for example.” Meaning that all approaches took a considerable amount of time and effort to perform, with the end-to-end process on average lasting up to ten days with approx. 8-9 people on hand to support, not including the inspection itself and any follow-on actions.
“As time went on and technology progressed, robotically-operated cameras were introduced to reduce the time it took to enter and inspect a tank”, Constantinis commented. With this, EM&I Alliance Group developed its robotically-operated ‘NoMan camera’ to enable the company, operators and surveyors to have a general overview of the tank, coatings and structural damage or corrosion. The high performance camera positioned on a carbon-fibre pole has zoom capabilities of up to 30-metres so it can provide a closer look at specific areas. It also has sufficient manoeuvrability allowing the camera to get into confined places within a tank onboard an FPSO.
The NoMan camera’s control unit and screen is protected by a habitat, an enclosure in which non-explosion proof equipment can be used within a hazardous area, which makes the camera gas safe and suitable to enter tanks onboard nuclear platforms as well as traditional offshore assets. The camera, which has its own lighting, is controlled by an EM&I operator outside of the tank and is technically regarded as a ‘remote’ form of technology, meaning surveyors and crew members do not need to enter the confined space, improving the safety of the activity and importantly, limiting the need for physical entry, and working at height, taking personnel out of an unnecessary hazardous situation.
“When using the NoMan camera, the tank still needs to be cleaned but only to remove excess sludge, making sure areas of concern are visible rather than preparing it for human entry, which can save the operator and its crew time on preparation and planning ahead of the inspection.”
Images courtesy of EM&I Alliance.
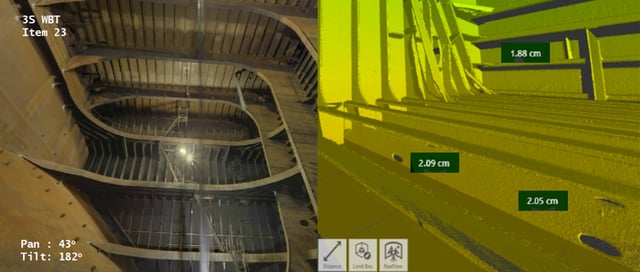
So, what about Class?
In line with LRQA's key role in the offshore world – ensuring floating assets are fit for purpose from construction, in-service to decommissioning – LRQA worked with EM&I to provide a basis of ‘what good looks like’ for the NoMan camera, outlining what needs to be inspected and at what level of detail, as the camera’s results directly feeds into the RBI plan agreed for that specific facility.
Providing a greater level of insight and data about the tank, the NoMan camera can also improve LRQA's and the operator’s understanding of that specific facility, enabling better decisions around planned maintenance, by looking at specific areas rather than the entire asset, and if appropriate extend the life of an asset when it comes to redeployment.
A collaborative approach
LRQA is also part of HITS joint industry project (JIP) which is an international initiative that aims to improve the way the industry manages the integrity of marine structures such as FPSOs, FSRUs, FLNGs and other floating offshore assets. The JIP is now in its seventh phase which looks to stop human entry for tank inspections, through technologies such as the NoMan camera. Founded by EM&I in 2011, HITS is supported by operators, regulators, classification societies as well as service providers and has successfully delivered industry innovations and guidance related to improving hull inspection, enabling shared knowledge throughout the industry and awareness around key issues.
How does it work?
Throughout the inspection, a surveyor located outside of the tank instructs the EM&I camera operator of the specific areas that need to be inspected. Referring to the agreed RBI plan for that facility, the surveyor can identify areas they suspect to be corroded or cracked, for example. If this is not the case, it could postpone maintenance. Alternatively, if more corrosion is found, surveyors and crew can expediate repairs and maintenance, enabling the operator to make robust decisions and plan effective maintenance, all of which having limited impact on operations.
“This leads to a very focused inspection, rather than inspecting the whole tank, the traditional way, making the process more efficient – saving time and money for the operator,” said Constantinis.
By using the NoMan camera, surveyors and crew can take stills that capture the exact time, date and location within the tank, providing realistic depictions that can be used for comparison at a future inspection by a different LRQA surveyor and inform decision-making by the operator at a later stage if repairs are needed.
“Ongoing developments of NoMan include specialised laser scanning cameras which will provide additional information on structural condition” added Constantinis.
Next steps
Currently, the NoMan camera can provide surveyors with a clear view of the inside of the tank but it cannot measure thickness or the distortion of components – so determining how thick a metal plate is or whether it’s getting thinner or is starting to bend cannot be performed by NoMan.
EM&I are now developing synchronous laser scanning technology for the NoMan camera system which can scan the tank and provide distortion information and thickness readings. This dimensional information can then be used by surveyors to understand the state of the tank, identify corrosion or other damage and determine which materials/areas/equipment need to be replaced. Importantly, by providing realistic data, the NoMan camera can help surveyors and operators understand the structural integrity of the facility, by feeding into the asset’s RBI plan, making planned maintenance more efficient.
From a class perspective, LRQA will provide guidance to EM&I on what areas of the tank need to be inspected using the synchronous laser scanning technology and the correct data needed by surveyors to determine if there’s any corrosion or damage. This is in alignment with LRQA's guide, “Remote Inspection Technique Systems (RITS) Assessment Standard for use on LRQA Class Surveys of Steel Structure”, which sets out LRQA's expectations on what RITS such as the synchronous laser scanning technology should achieve. If approved, operators will see through LRQA's third-party validation that the technology is doing what it’s supposed to do, and regulators can see that LRQA and EM&I continue to work in line with best practice, industry standards and latest guidance associated with hull integrity and tank inspection.
From a regulatory perspective, LRQA continues to work with regulators to ensure they have confidence in the latest inspection technologies, which are in line with LRQA's RITS Assessment Standard and consequently, the offshore industry makes progressive steps to ensure assets are verified as safe while where possible also remove personnel from hazardous environments.
By utilising data from technology such as the NoMan camera and synchronous laser scanning, class societies, inspection companies and operators should reach a point where all parties involved can see patterns over time, significant structural issues with the design, for example, and actually determine what the change means rather than see change simply occurring.
As to the future, Constantinis is optimistic about the NoMan camera system. “EM&I’s ambition going forward is to develop software or some sort artificial intelligence which will recognise and eventually predict patterns over time, such as coating damage, instead of reviewing hours and hours of video.”
Going forward, this data will support the offshore industry’s eventual move to artificial intelligence and digital twins, informing key decision-making with regards to potential redeployment opportunities and life extension.